The quote below is from Dr. Gary White’s website, http://whitemuzzleloading.com/green-river-rifleworks/2/
The stocks started life as a plank, kiln dried and 2.5 to 3 inches thick. The planks were bandsawed into blanks, then cut to rough size on a modified furniture carving machine. Later GRRW acquired a rotary 4 place machine that did a more consistent job. Once 5 axis panto-graphs were developed, GRRW switched to purchasing the carved stocks outright. Nowadays, CNC panto-graphs are used for the same purpose. Once the stock was rough carved, the barrel channel was cut, cuts for tang, butt plate and lock were milled in with small individual panto-graphs.
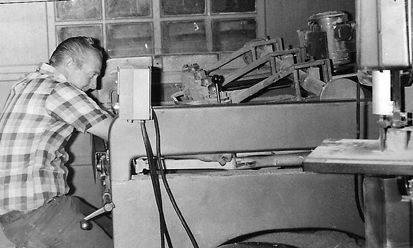
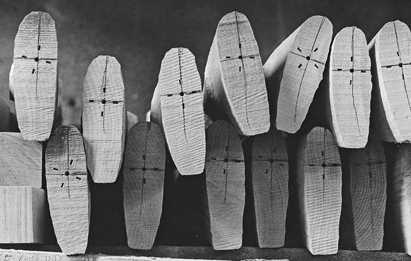
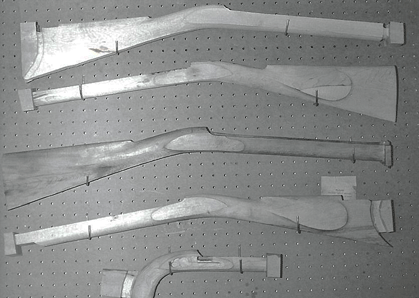
Charley Winn is shown in the photos to the left working at the stock duplicator.
The two photos to the right show shaped stocks ready for the next steps of cutting the barrel channels and drilling the ramrod holes.
On the early stocks, the ramrod hole in the forearm was cut out with a router after cutting the barrel channel as seen in the photo above.
This was done to speed up the process and eliminate the chance of the drill bit wondering out the bottom of the forearm or up into the barrel channel or to one side or the other while drilling the ramrod hole. In addition to saving time, it also prevented having rejects due to off center ramrod holes.
This was a common technique in pre-carve stock making in the 1970’s, and did not affect the structural integrity of the stock in any way. The GRRW rifles in my collection with this groove in the forearm have as snug a fit to the barrel as the rifles without the groove. Some of these rifles show heavy use from many years hunting as well as time at the range and the rendezvous.
With the barrel channel cut and the ramrod hole drilled, the stock was ready for the rifle stockers to begin inletting and fitting the metal parts.

By 1976, GRRW was purchasing some pre-carve stocks from other suppliers. Ron Paull shared a section of his personal record book of his builds while working at GRRW in late 1976. This entry for full stock Hawken SN 23 has a notation that it used a pre-carve stock from Frontier Carving Shoppe.
The Frontier Rifle Shoppe ad to the right ran in the February 1972 issue of Muzzle Blasts. They appear to be an early supplier of pre-carve stocks, and include Pennsylvania longrifle stocks in their product line.
It makes sense that GRRW was purchasing full stock pre-carves since their panto-graph was big enough for duplicating half stocks only.
GRRW was advertising kits for the Leman Trade Rifle that had fully shaped and inlet stocks in 1978. By early 1979, they were advertising both the Leman Trade Rifle and Leman Indian Rifle kits with completely inlet and fully shaped stocks.
In 1979, I purchased a Leman Indian Rifle kit. The invoice has a notation that indicates that GRRW obtainied these completely inlet and pre-shaped stocks from Reinhart Fajen.
I later purchased a half stock Hawken kit and a full stock Hawken kit from GRRW. The stocks in those kits were rough shaped from the lock panels back and left square in the forestock. The barrel channel was cut and the ramrod hole drilled, but with no inlets.
Considering the limited amount of wood removed and the very large and course router tool used, these stocks may have been shaped in house.
GRRW also used jigs and mills or small routers to cut out much of the lock mortise. The marks from the circular cutter can be seen in the rifles lock mortise. Hand inletting was required for the final fitting of the lock in the mortise.
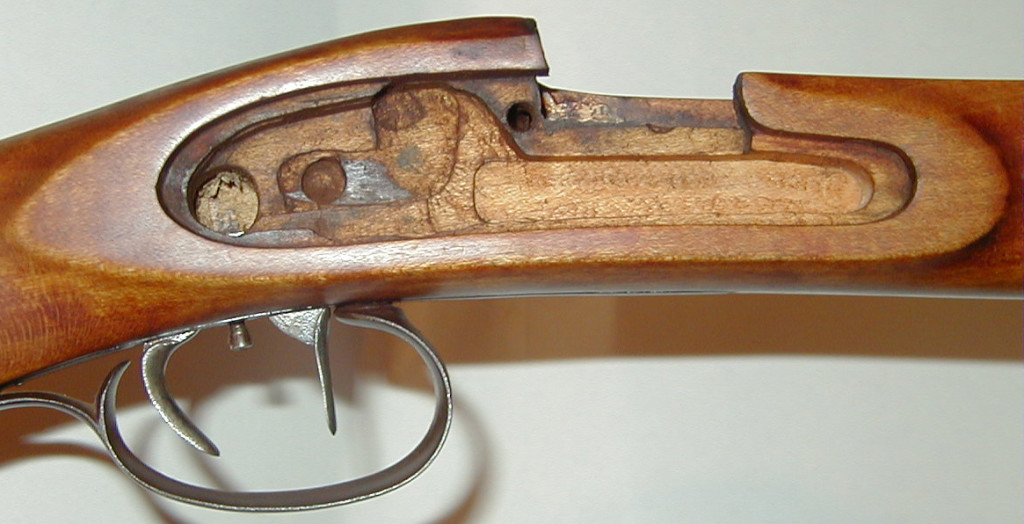
This appears to be something that was developed and improved over time because this earlier rifle shows signs of more hand tools.
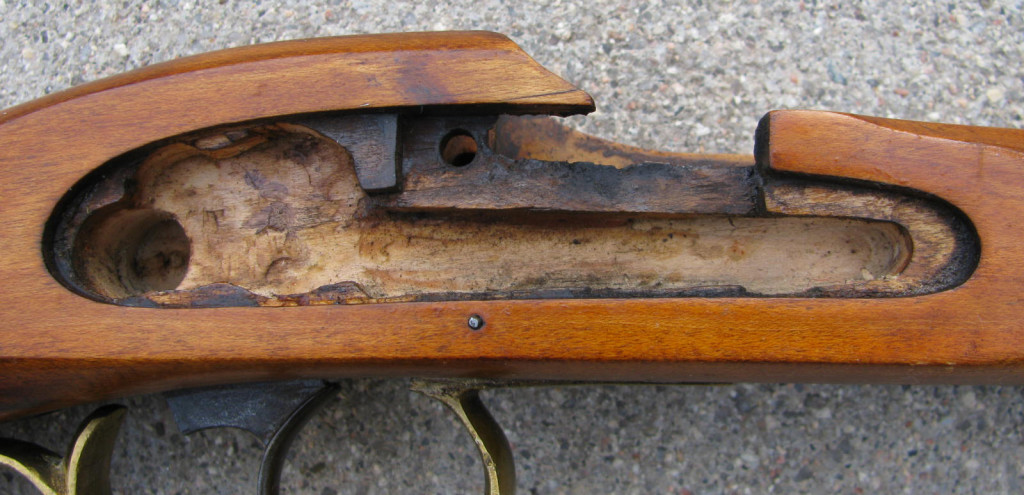
The process, as described to me by a former GRRW employee, entailed the use of a jig with a cutout that was placed over the stock and the mill or router followed the cutout to form the mortise.
This would work for the lock plate, but the lock mortise is more complex with areas of different shapes and depths for the springs, tumbler, and bridle. If a jig was laid over the stock and the mill followed the cutout of the jig, then a different jig would be needed for each of the smaller cutouts and adjusted for each depth.
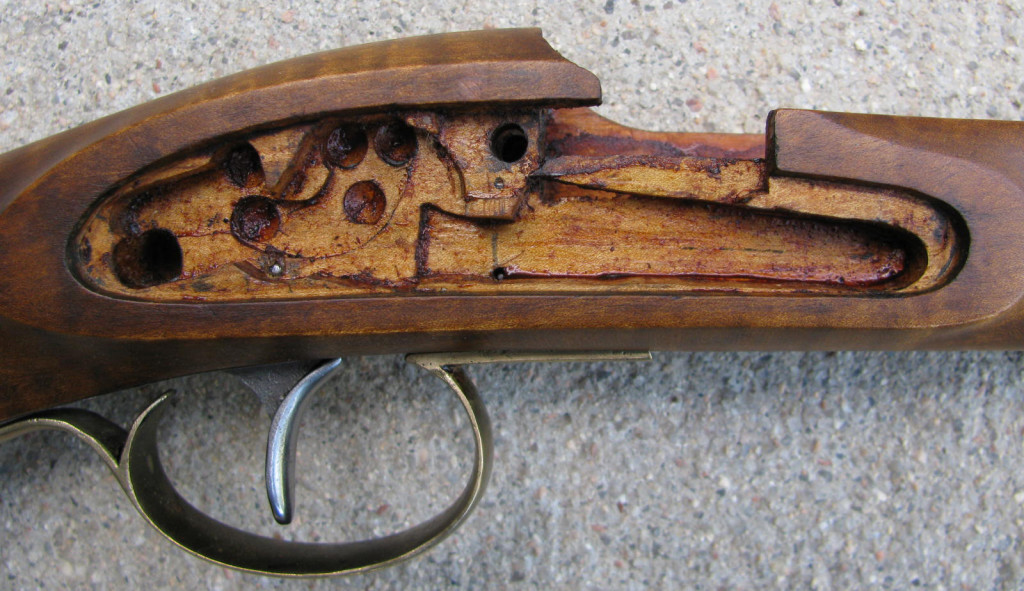
This picture from an article on Sharon Rifle Barrel Co. shows how they pre-inlet the tang on their Hawken kits. This type of technology was common in the gun industry in the 1970’s and something similar could have been used at GRRW for the complex lock mortise. In fact, Doc White says they did in the quote at the beginning of this article when he states:
…cuts for tang, butt plate and lock were milled in with small individual panto-graphs.
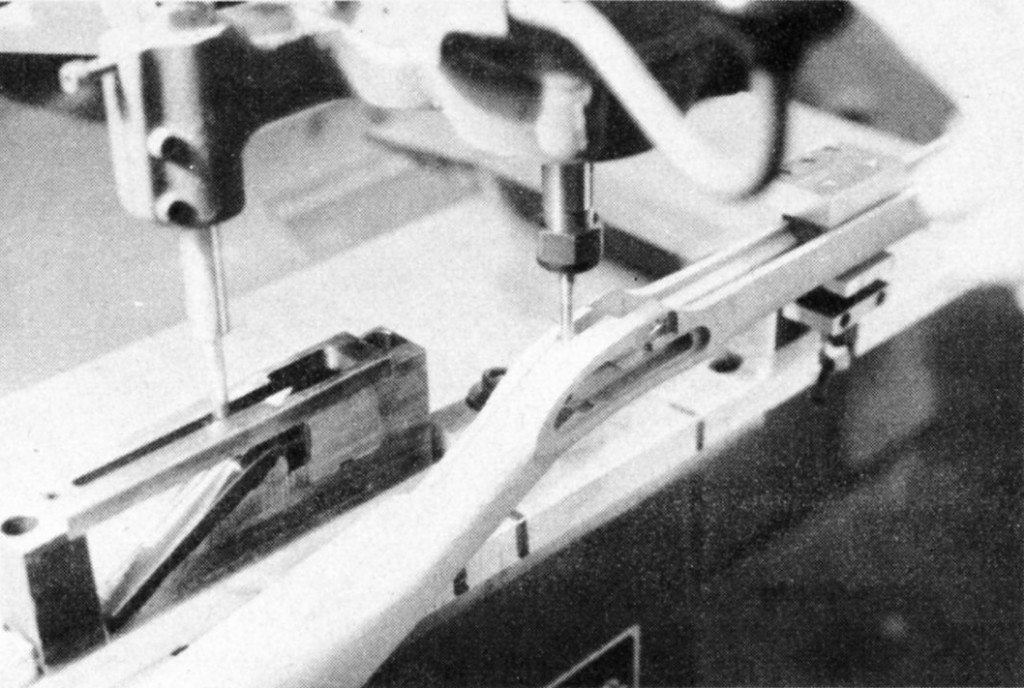
Which ever method was used for the lock mortise, it is interesting that they never utilized as many labor saving techniques on the Hawken rifle as they did with their Leman rifles. There is no indication that GRRW ever attempted to use completely shaped and inlet stocks with their Hawken rifles like they did with the Leman rifles. They may have wanted to offer the customer more options to customize the Hawken instead of restricting the customer to a predetermined set of component parts.
The net result was that inflation had a much bigger impact on the price of a standard half stock Hawken than it did with the half stock Leman. The 1973 and 1979 catalog prices for factory finished Hawken and Leman rifles and the kit versions are shown in the table below. The factory Hawken was 63% more expensive than the Leman in 1973 and 81% more in 1979. The Hawken kit was the same 63% more than the Leman kit in 1973, but by 1979, the Hawken kit was only 42% more than the Leman kit.
Model
1973
1979
Percent Increase
Factory Hawken
$324.95
$725
123%
Factory Leman
$199.95
$400
100%
Hawken to Leman Ratio
63%
81%
Hawken Kit
$194.95
$269
38%
Leman Kit
$119.95
$190
58%
Hawken to Leman Ratio
63%
42%
The fully shaped and completely inlet Leman stock from Reinhart Fajen contributed to the increase in price of both the Leman kit and factory Leman, but it saved in-house labor costs. What is really striking is that the Hawken kit went up 38% from 1973 to 1979 while the factory finished Hawken increase by 123%. This was the period of high inflation and Cost of Living Allowances, and the cost of labor involved in stocking the Hawken was increasing much more than the cost of parts.
Back to How They Were Made